
All-in-one solution for automated production of copper fittings
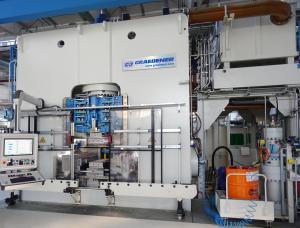
The fully automated production of copper fittings on the Graebener® fitting press enables very short cycle times
Hydroforming specialist Graebener makes fittings production even faster, more flexible, and more cost-effective
NETPHEN, NORTH RHINE-WESTPHALIA, GERMANY, May 7, 2025 /EINPresswire.com/ -- Thanks to 40 years of expertise, the custom machine builder Graebener is one of the most trusted experts in hydroforming worldwide. The company's machines for internal and external high-pressure forming are used in the automotive, hydrogen, and fittings industries. For the fittings sector, the company initially developed presses with internal high-pressure forming for steel fittings. In recent years, the market has been increasingly demanding machines for the production of copper fittings. One reason for this is the increased switch from soldered to press fittings, for example in the US. Graebener supplies machines that feature three innovations: shorter cycle times with new automated loading and unloading, a faster tool change system, and production of the entire range of copper fittings, including special sizes, on a single machine.Across most of Europe, the conversion from solder fittings to copper press fittings, which are much faster to process, has long been completed. Several other countries beyond Europe, including the US, have now recognized the advantages and are converting their machines. In response, Graebener has specialized in tailor-made presses for copper fittings and incorporated several of its own innovations that make production even faster and more flexible while reducing innovation costs.
Entire product range including special dimensions on one machine:
The Graebener® fitting press for copper fittings is equipped with a maximum closing force of 8,500 kN and enables the production of all fitting designs on a single machine. A new feature is that press fittings with the special dimensions of 2 x 1/2 x 2 inches can now also be produced on the press for the first time. Previously, this design was only available on the market as a solder fitting with a very short dome. Graebener has now succeeded in manufacturing this extreme size with a long dome – suitable for pressing – and without any wrinkling.
Automated loading and unloading with faster cycle times:
Another innovation is the automated feeder system, which enables series production with even shorter cycle times. The system integrated into the control system contains not just one feeder (slider), but rather two: one slider for loading and one for unloading. The separation of loading and unloading ensures more flexibility and higher productivity. Automatic component detections by means of sensors simultaneously indicate whether all components have been correctly loaded or ejected.
A robot-compatible interface concept is also an integral part of the system. Thus, the feeder can be loaded either fully automatically directly from the coil via robot or whenever required manually. Robot loading therefore reduces cycle times even further. Depending on the fitting size, up to 20 components can be produced in 16 seconds.
Tool change system for shorter machine downtimes:
The third innovative development enables a significant reduction in tool change times: Each multiple tool change requires manual alignment of the sealing mandrels. This is usually done inside the machine with the tool installed and in confined spaces. The process usually takes several hours, during which the machine is at a standstill. Graebener has now designed a system that allows the mandrels to be aligned outside the machine while the machine continues operation.
Each system consists of two identical tool change blocks, which serve as the base for the tool, and various customized forming tools that are inserted into the blocks. This means that while the machine is in production, the next tool can be prepared outside of the machine. Once the first production run is completed, the entire tool block, including the tool insert, is exchanged and the second production run can begin immediately.
On the safe side for over 40 years:
Graebener is one of very few companies worldwide with over 40 years of expertise in hydroforming. Continuous research and development - not least in its own hydroforming prototyping center - has made the company a leading supplier with outstanding technical expertise and process understanding. Thanks to the in-house prototyping systems, new customer solutions can not only be developed but also tested without risk.
Furthermore, Graebener® systems including water or oil hydraulics, electrics and control software are of modular design. Existing systems can therefore be retrofitted easily and cost-effectively. Even converting simple hydraulic presses to high-pressure forming systems is possible without any problems.
For customers with limited space, a customized solution with a compact design can be implemented. The HFA system, including pressure intensifier, is then installed in a compact unit underneath the hydraulic tank. The suction tank is located above the machine to ensure high closing speeds.
Graebener's own PressPro® control and regulation concept is also provided. This contains interfaces for data recording, which can be displayed visually. Depending on their password level, operators also have the option of creating their own programs, implementing changes, as well as optimizing parameter settings.
Frank von der Heyden
Gräbener Maschinentechnik GmbH & Co. KG
+49 27379890
f.vonderheyden@graebener.com

Distribution channels: Automotive Industry, Companies, Energy Industry, Manufacturing, Waste Management
Legal Disclaimer:
EIN Presswire provides this news content "as is" without warranty of any kind. We do not accept any responsibility or liability for the accuracy, content, images, videos, licenses, completeness, legality, or reliability of the information contained in this article. If you have any complaints or copyright issues related to this article, kindly contact the author above.
Submit your press release